Quick Contact Request
Please fill in information below and we will be in touch shortly.
Built for Speed: The Future of Domestic Electronics Contract Manufacturing
February 12, 2017 by Philip P. Thurman | News
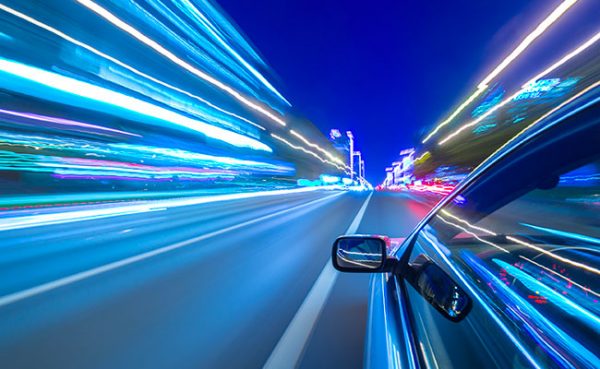
Even though domestic manufacturing favorability has recently increased, supply chain locality and cheap labor should continue entrenching consumer mass production electronics abroad. However, the market for B2B prototyping, preproduction, and midrange, high reliability domestic electronics contract manufacturing should remain relatively stable for the foreseeable future. Anyone remotely involved in either the design or manufacturing of electronic circuit boards in today’s industry recognizes market trend evolution of accelerated responsiveness and execution, platform consolidation, time to market sensitivity, and obsolescence awareness. Dr. John P. Kotter, Konosuke Matsushita Professor of Leadership, Emeritus at Harvard Business School writes:
“The hierarchical structures and organizational processes we have used for decades to run and improve our enterprises are no longer up to the task of winning in this faster-moving world. In fact, they can actually thwart attempts to compete in a marketplace where discontinuities are more frequent and innovators must always be ready to face new problems.” (Kotter, 2012, p. 46).
Electronics Manufacturing Services (EMS) providers are mechanistically structured by nature to ensure inputs generate process repetition resulting in the highest quality, lowest cost output. However, the need for speed demanded by larger companies outsourcing their assembly requirements is exponentially increasing and adaptation is forcing a shift towards more organic approaches. The key to success will be those organizations who adopt enough of an organic structure for rapid response but retain enough of the mechanistic elements ensuring process control, repeatability, and subsequent value generation. Quality Manufacturing Services personifies industry leadership recognizing and applying this developing future reality.
Change is a fact of life and business, especially in technology related industries such as circuit board assembly manufacturing. An effective contract manufacturer can no longer operate under isolated departmental silos of the past, adhere to strict centralized command and control, and avoid workforce empowerment if competitive edges are to be maintained. Due to the most recent global economic downturn, OEMs are compelled to compete with continuous stakeholder value improvements to do more with fewer financial and other developmental resources and less time. Logically, these same demands flow down to EMS providers who, in turn, flow this demand down to the component and raw material levels.
Technology advancements affect a continuous dynamic influence upon EMS strategy. Developing package device sophistication allows entire platforms once composed of multiple printed circuit card assemblies to now consolidate into a single hybrid integrated circuit. 3D printing innovations are redefining material and design restrictions to now occur in a matter of hours while the same demand once required weeks or months to accomplish. Chip component packaging has miniaturized to such a microscopic level that these devices now receive an operator warning notice to handle as dangerous airborne inhalants.
Specific tools may be applied to ensure organizations are optimally sustaining competitive edges through application of the McKinsey 7S (Peters & Waterman, 1984) framework or strategically approaching transformation efforts through J.P. Kotter’s (2012) Eight Stage Change Initiative Process. Organizational benchmarking against these two standards enables EMS providers to enact mechanistic to organic limited transitioning while not losing sight of the mechanistic features sustaining original quality and reliability. A current and future EMS provider understands that competitive edges are no longer exclusive to superior customer service, quality, on time delivery, and other standard organizational performance metrics. These are fundamental, expected preconditions of a sustained professional relationship. EMS competitive edges of the future will continue generating value while adapting to increasing responsiveness requirements. The following eight traits reflect mandatory characteristics requiring cultural execution for all future EMS activity:
1) Transformation into a learning organization receptive to industry shifts acknowledging strategic adjustment for competitive edge maintenance
2) Selective mechanistic to organic transitioning to optimize flexibility and adaptation
3) Elimination or adjustment of mental models, preconceived bias of past methods of success based upon historical linear thought problem solving
4) The encouragement of controlled risk-taking and experimentation with the recognition of inefficiency sacrificing short term gains but yielding long term benefits
5) Concept initiation partnerships between customers, supply chain, and manufacturing equipment developers to ensure skill maintenance of most current industry capability expectations
6) Strict financial stewardship enabling consistent asset alignment
7) Recognizing and embracing automation wherever possible
8) Leveraging information technology for both internal and external advantage
The demand for speed in quoting, manufacturing, and delivery will not ease in the foreseeable future and, if anything, should exponentially increase. Deloitte Consulting observes that “With the greater use of digital manufacturing tools, an increasing number of physical objects being digitized, and a growing number of processes digitally transmitted and managed, the speed of evolution and collective learning increases, in turn speeding the fragmentation process.” (p. 36) Successful EMS providers of the future will sustain a structure identifying those leading indicators that identify obsolescence fragmentation and restrategize so “leaders have the opportunity to use deep understanding of these drivers to anticipate potential changes. They can then move their business in a direction both congruent with market forces and designed to position their company favorably.” (Hagel, Brown, Koolasuriya, Giffi, & Chen, 2015, p. 37).
The globalization of competition and instantaneous international communication is forcing leaner, more nimble organizations to either recognize and adapt or cease to exist. If a company does not stay ahead of the industry snowball demanding organizational learning behaviors encouraging adaptation, strategic adjustment, and flexibility, it will eventually run over them.
Reference:
Hagel III, J., Brown, J.S., Koolasuriya, D., Giffi, C., & Chen, M. (2015). The Future of
Manufacturing: Making Things in a Changing World (PDF). Deloitte University
Press. Retrieved from https://dupress.deloitte.com/dup-us- en/industry/manufacturing/future-of-manufacturing-industry.html
Kotter, J. P. (2012). ACCELERATE! (cover story). Harvard Business Review, 90(11), 44-58.
Kotter, J.P. (2012). Leading Change. Boston, MA: Harvard Business School Press
Peters, T. J., & Waterman, R. H. (1984). In Search of Excellence : Lessons from America’s Best-Run Companies (Warner books ed.). New York, NY: Warner Books.
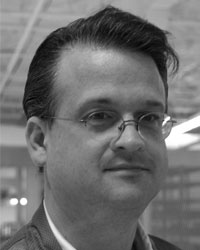
Philip P. Thurman
Phil is currently the Quality Assurance Director for Quality Manufacturing Services, Inc. and has been a manufacturing quality assurance executive for 30 years with extensive experience in military power management systems, electronic manufacturing services, and quality systems applications. Receiving a BA in English from Stetson University and an MBA in Organizational Leadership from Norwich University, he is a published author and often consulted for electronic systems manufacturing development guidance. His extensive knowledge offers unique insights into industry trends, manufacturing advancements, and the continuing role of quality assurance evolution relative to technological progression.