Quick Contact Request
Please fill in information below and we will be in touch shortly.
COVID-19 Pandemic: The Past, Present, and Future
May 10, 2021 by Philip P. Thurman | News
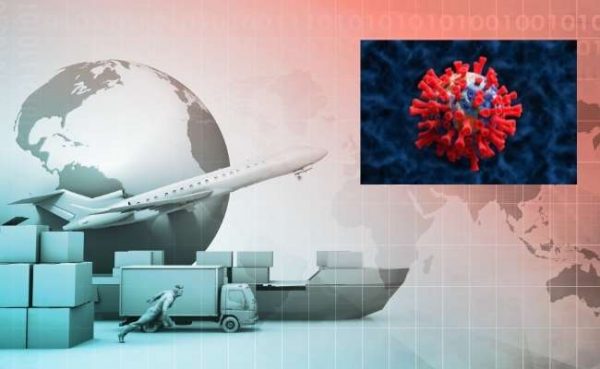
Supply Chain Raw Material Shortages and Rare Earth Metal Constraints are Skyrocketing Electronic Manufacturing Component Lead Times and Costs
During the transition period between initial awareness of COVID-19 and realization as a global pandemic, individual reactions varied from the virus as nothing more than a mild flu all the way to a second coming of the Bubonic plague. Fully more than a year after the initial spread, not a civilized person exists without the event’s influence on some personal level. After affecting the entire global economy, moderating restrictions, widespread vaccine administration, and other pandemic easing signals are welcome positive indicators. Even toilet paper’s brief stint as the new Gold Standard is now just an unpleasant memory. The COVID-19 worldwide shutdown will be felt for decades if not a generational overshadow highlighting supply chain fragility. In relationship to industry pressure, the most accurate perspective can be divided into three distinct waves:
First Wave: Labor Suspension (Past)
Second Wave: Supply Chain Disruption (Present)
Third Wave: Quality Decay (Potential Future)
Ebbing influence remains over the first wave with most recent patterns showing a slow but ramped recovery. Collaborating with our partners, several steps may be taken in the business-to-business electronics manufacturing industry to minimize the second wave’s current global supply chain shortage and associated cost increases. Shortages are not just restricted to well-publicized integrated circuits. Sudden scarcity has developed across the range of both active and passive devices in addition to significant price increases for bare printed circuit boards and solder. Finally, the potential quality decay risk last wave is something we had better acknowledge, prepare for right now, and establish strategic planning so electronics manufacturing service providers don’t become caught in the undertow.
First Wave – Labor Suspension
Employment loss was the first significant economic pandemic devastation. Normally busy streets were emptied and gasoline even fell below one dollar a gallon in many areas. Businesses scrambled work from home strategies and most service industry workers were told just to stay home. The approach was functional for information-based models but the alternative doesn’t quite work for manufacturing’s hands-on necessity. In April 2020, United States unemployment reached 14.8% according to Congressional Research Service. During this same month, almost two million manufacturing jobs were lost (BLS, 2020). As local and Federal governments gathered knowledge and made the most proactive possible day to day decisions based upon Center for Disease Control guidance, the economic standstill, regardless of industry, full or part time, education level, or other demographic, impacted everyone to some degree. Foundries, stamping presses, and wire bonders all fell silent. Unless you were deemed an “essential” worker, personnel were told to stay home who normally operated integrated circuit assembly equipment, processed compositional material for passive components, or etched raw panels into printed circuit boards (mostly domestic).
Second Wave – Supply Chain Disruption
Whether your market is construction, food distribution, or electronic components, almost every operating industry today has been disrupted to various magnitudes with the supply chain shortages we all now encounter. Decades of maximized profit margins through off-shore procurement ultimately resulted in a situation only worsened by the pandemic. But the United States isn’t suffering alone. Our globally interconnected economy is feeling hardship not defined by international borders. According to William Boston of the Wall Street Journal, “Global auto makers who had expected the semiconductor supply crisis to subside in the spring are now warning that chips will remain scarce for months while a second-half recovery is fraught with uncertainty.” (Boston, 2021). The need for domestic supply chain reshoring is obvious. However, hindsight prevention is without meaning relative to the reality challenge we all currently face. Electronic assemblies, components making those devices, rare earth metals, polymer substrates, and composite inorganics used in their construction are experiencing an unprecedented lack of supply in the modern era.
The automotive industry, Internet of Things, increasing automation, and personalized electronics are squeezing an already thin amount of available material. Limited inventories are tightened even further as warehouse lights are just now turning on again and original component manufacturers (OCMs) reestablish and attempt production schedule acceleration. Integrated circuit supply suffered even further with Texas weather-related shutdowns, the Japanese Renesas factory fire just over a month ago, and cold weather events in the Eastern United States this past winter. Regardless of what may appear a monumental challenge in fulfilling customer delivery requirements, several strategies exist. The relative effectiveness of each centrally relies on the partnership strength already established with those you serve. These approaches are a mutually beneficial and balanced commitment of potentially burdened risk with potential uninterrupted customer supply rewords.
1) Customer Cost Sharing on excessively high Cost of Goods Sold (COGS) Components
After necessary components are located, high COGS items may be prohibitive to order all at once to maintain inventory for current or immediate future needs. Make arrangements with your customers to possibly share the financial burden with potential associated overall assembly cost reduction incentives and staggered deliveries.
2) Urge customers to place orders quick as possible to get the supply chain pipeline in motion
The faster you can get the supply chain pipeline moving, the faster your responsiveness to meet delivery commitments. Possessing the earliest possible visibility to needs is essential. Request that customers attempt anticipating their demand as soon as possible with the understanding that you can’t react until they do. Nobody wants to sit on hundreds of thousands of electronic assembly inventory dollars only to wait another eight weeks after everything has already been received for a half cent ceramic capacitor.
3) Secure Letters of Authorization
If suppliers have legal guarantees of commitment for a specific commodity at a specific spot price, both distribution and OCMs are also provided with the same visibility you request of your customers. Capital allocation, manpower, and other supporting resources are easier to manage once the commitment is established from vendors with a solid history of reliability.
4) Incentivize suppliers/distribution
Like sharing the burden of high COGS with your partners, offer guaranteed incentives to both distribution and OCMs. Commit to a defined time frame for sourcing exclusivity or financial discounts based upon acceleration of delivery or allocation.
5) Lowering inventory turns/Creative Stocking
Nobody likes excess inventory for the obvious associated costs. However, certain situations or climate shifts to parity occur where the cost of not getting an order due to long lead time generated from material shortages exceeds the costs associated with excessive inventory burden. Working with your internal supply chain management, strategize those items with excessive shortages, establish percentages of surplus, and continuously monitor status changes with your suppliers in relationship to customer pull-in demands. Also, consider the potential of Kanban or other Push Pull stock strategies.
6) Request customer product design with as much sole source avoidance as possible
This mindset hopefully exists regardless of industry climate. But especially during this era, the less sole sourcing translates to increased flexibility for all inputs into assembly realization. Supply chain, production, quality, finance, and every other product manufacturing chain element reduces burden when component selection alternatives are maximized. Obviously, certain applications and design requirements demand specialty sourcing. When more available alternatives exist with the most minimal risk, make best judgements in bill of material consideration. Explore expanding end of life assembly termination dates as stop gaps until material becomes more readily available for newer system introductions.
7) Customers pursue incentives from OCMs with commitment to incorporate their devices
Component manufacturers, like any other business, exist to maximize profits. Design and development should establish clear channels with OCM marketing departments and positions of sourcing commitment. This mutual trust is established when you commit to designs utilizing only their devices as primary functional support and they make return promises that lack of inventory will never affect your ability to fulfill dock dates.
8) Allocation guarantees
Like OCMs, distributors also want to maximize profits while maintaining the lowest possible inventories. Secure legal contracts guaranteeing that certain component volumes will be set aside and pricing locked with promise of future consumption. We all understand the risk involved in perspective respect of budget constraints and timing, especially Federal contracts. But, like shared COGS risk consideration, allocation positioning implies shared risk of potential excess inventory. Work with your supply chain and customers to mutually identify the threshold where spot price availability or schedule is considered of most critical concern.
Third Wave – Quality Decay
You control the third potential wave. After labor and material returns, orders are still going to need fulfillment. But by this time, weeks and months may have passed since the original commitment. The Third Wave will bring increased counterfeiting frequency, dubious pedigrees, inadequate storage conditions, unsafe preservation packaging, and mechanically compromised components. At this moment, vigilance and discipline are the only characteristics of your organization preventing damage to customer relationships. No matter the temptation to accelerate through the manufacturing cycle, pressure to shortcut steps, or even external threats, follow your quality management system with unwavering discipline. Do not fall for your competitor’s temptation to drift away from your company’s core convictions or surrender to less than best practices. Ensure the personal commitment of excellence from every team member. If your product doesn’t fulfill your customer’s expectations, not enough processing time savings compensate for repeating the work, sacrificing integrity, or even worse, positioning your customer with integrity loss damage from their customer. If you maintain the necessary steps to produce a good product regardless of industry pressures, you protect both yourself and your customer. In the end, customers will thank you, the test will strengthen your partnerships, and everyone gains increased value.
The COVID-19 pandemic impact is unprecedented. Although the Spanish Flu may be proven as more deadly, the global community was not as industrialized and interconnected, therefore we did not experience quite the same impact as COVID-19 upon our current times. The electronics manufacturing service industry will endure through these challenges. By now, you should be well past global pandemic strategy integration into your business continuity plan. Like any other industry challenge, the path towards reemerging on the other side intact is clearest possible communication, honesty between partners, and always keeping customer best interests in consideration of every business decision.
Reference:
Falk, G. et.al. (2021), Unemployment Rates During the COVID-19 Pandemic: In Brief (PDF). Report R46554. Retrieved from https://fas.org/sgp/crs/misc/R46554.pdf
Anon., (2020). News Release #USDL-20-0815 (PDF). Bureau of Labor Statistics.
Retrieved from https://www.bls.gov/news.release/archives/empsit_05082020.pdf.
Boston, W. (2021), Global Chip Shortage Set to Worsen for Car Makers. Wall Street
Journal. Retrieved from https://www.wsj.com/articles/global-chip-shortage-set-to-worsen-for-car-makers-11619708393
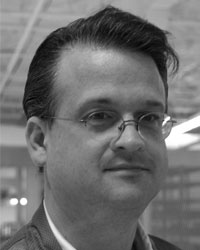
Philip P. Thurman
Phil is currently the Quality Assurance Director for Quality Manufacturing Services, Inc. and has been a manufacturing quality assurance executive for 30 years with extensive experience in military power management systems, electronic manufacturing services, and quality systems applications. Receiving a BA in English from Stetson University and an MBA in Organizational Leadership from Norwich University, he is a published author and often consulted for electronic systems manufacturing development guidance. His extensive knowledge offers unique insights into industry trends, manufacturing advancements, and the continuing role of quality assurance evolution relative to technological progression.