Quick Contact Request
Please fill in information below and we will be in touch shortly.
What a Disaster: Business Continuity Strategies when Dealing with Mother Nature
February 26, 2018 by Philip P. Thurman | News
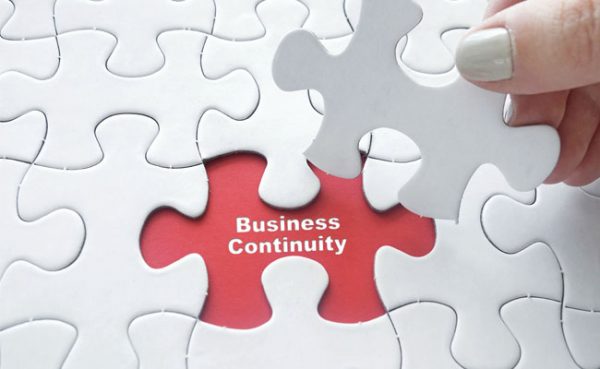
While employees may call in sick, your company cannot. No disaster recovery and business continuity examination can explore every potential scenario or prescribe a universal approach but two common references exist in every effort – scope and time. Even though the following focuses on small to midsize, single facility businesses, certain applications remain relative to all business types and sizes, each appropriately scaled. As an electronic manufacturing services (EMS) provider, Quality Manufacturing Services, Inc. understands customers having critical resources aligned in anticipation of delivery schedule commitments. In addition, potential late delivery fines or other legal penalties if those obligations go unfulfilled. Weather, disasters from either nature or man, or other force majeure events cannot and should not interrupt customer expectation fulfillment. In the United States alone, 2017 consistently experienced hurricanes, droughts, wildfires and floods. According to C. Mitchell of Accuweather, the cumulative cost was $306 billion in damage (2018).
Initial assessment begins with defining different scenario likelihoods and impact scopes. If located in the Southeastern United States, the chances of hurricanes are a more likely potential impact as opposed to the Western half of the country where wildfires or earthquakes are more frequent. The Northeast normally experiences at least one crippling blizzard a year halting most commercial transportation. Business disruption does not require an epic scale. The most common threat to operational continuity is prolonged electrical outage. Even though infrastructure remains intact, electricity is every company’s lifeblood and controls the ability to produce goods and services. Onsite back-up generators or mobile industrial generators are essential for power loss extending days, weeks, or longer. A wide variety of power, cost, and fuel type are available.
More significant impacts may include partial structural damage or complete loss. A practical approach to this extreme is partnering with a trusted ally in the same or similar market, establishing a capital sharing agreement in the event of a structural catastrophe. An ideal candidate location would exist geographically beyond the reach of the originating event. A well-defined, practiced, and tested interface team is also necessary to execute preexisting emergency protocols and ensure the entire organization understands necessary functions and expectations minimizing business disruption.
Once a potential event triage has been classified according to likelihood, the next analysis aspect defines the contingency steps taken during the initial twenty-four hours, the first week, the first month, or even longer. This concern may be minimal for large, multi-site companies but for small to mid-size single site companies, contingency plans are imperative to survival. Organizations must decide what infrastructure considerations are most operationally critical. These basic considerations are common to every business plan:
Employee Safety
While business continuity is essential to sustain customer commitments, no recovery plan should ever sacrifice the utmost commitment to employee safety.
Through all planning and anticipation, never lose sight that the reason for success, your employees, remains the most critical consideration. Depending upon severity, disasters not only impact business activities but also affect your employees’ daily routines and inflicts psychological impacts. Just as with your business, there is a disruption of mental model comfort, loss of basic amenities and power, and the need for a return to consistency. Every disaster recovery and business continuity plan’s most essential execution first considers employee physical, mental, and emotional safety. Time necessary for recovery depends upon the disruption level or in more extreme cases, catastrophic devastation.
Internal and External Communication
Clear and direct communication sustains continuity. Whether a siloed or flattened organizational structure, electricity remains the operational conduit allowing e-mail and phone contact. Establish a command center. This may be nothing more than a location relatively unaffected by the disaster such as a hotel room or other power intact location with structural integrity. If the event disrupts business no longer than a few days, mass customer e-mailings regarding status should alleviate most fears. Auto messaging to internal employee cell phones regarding operational status should also occur in parallel. Customers want to know to the degree of disaster impact on product status and employees want to know schedule status resumption to continue supplying those products or services.
IT Data Storage and Retrieval
Scope and time are synonymous relative to data storage and retrieval. This includes financial data, intellectual property, and operational software. Routine physical and electronic backups must occur as a component of daily protocol with on and offsite storage. Cloud storage has diminished some concerns but certain hardware and other proprietary media should possess both physical and electronic storage redundancies. J. Gilenne (2017) suggests a more proactive approach through instituting a technical resilience program where “The objective…is to avoid disruption by focusing on proactive measures, innovative architecture design and operational excellence.” Purchase orders, inventories, technical configurations, and other data must remain accessible and manipulative. Informed communication continuously relies on immediate data access, significantly relieving customer fear.
Supply Chain Continuity
If you’re a goods manufacturer, power loss for less than a week should not be a significant disruption but if extending longer, arrangements must be made with standard commercial carriers such as UPS, FedEx, and others for material to be delivered to alternate locations and your products to be shipped from alternate locations. This same framework may be mirrored with customers who will demand the same information relative to delivering their products.
Planning
Finally, have a plan. While having strong customer relationships is one of the most critical competitive edges, don’t jeopardize confidence for lack of planning. If a partnering agreement has been established, their disaster recovery and business continuity plans must be reviewed to ensure maintained congruency. Formulate a specific contingency plan defining roles and responsibilities for immediate, mid, and long-term actions and hold accountability. Plan copies should be kept both on and offsite. Test the plan, audit the plan, and continuously improve the plan.
Today’s accelerated market competition demands product and service continuous flow performance regardless of external or internal influences disrupting organizational supply ability. No matter what business size or type, disasters do not alleviate an organization’s management from ensuring that continuous benefit is sustained for all stakeholders. It is the obligation of every management team to ensure the continuous operation of a business beyond the influence of individual presence or absence. Neither your employees nor your customers can take the risk of not fulfilling customer commitments – and that would be a disaster.
Reference:
Gilenne, J. (2017 August). How Digital Disruption Can Threaten Disaster Recovery Planning. Retrieved from http://deloitte.wsj.com/riskandcompliance/2017/08/14/how-digital-disruption-can-threaten-disaster-recovery-planning-2/
Mitchell, C. (2018 January). 2017 goes down as costliest year for weather disasters ever recorded in US. Retrieved from https://www.accuweather.com/en/weather- news/2017-may-set-all-time-record-for-most-billion-dollar-weather-climate- disasters-in-us-history/70003625
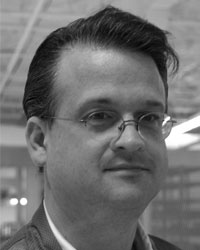
Philip P. Thurman
Phil is currently the Quality Assurance Director for Quality Manufacturing Services, Inc. and has been a manufacturing quality assurance executive for 30 years with extensive experience in military power management systems, electronic manufacturing services, and quality systems applications. Receiving a BA in English from Stetson University and an MBA in Organizational Leadership from Norwich University, he is a published author and often consulted for electronic systems manufacturing development guidance. His extensive knowledge offers unique insights into industry trends, manufacturing advancements, and the continuing role of quality assurance evolution relative to technological progression.