Quick Contact Request
Please fill in information below and we will be in touch shortly.
Miniaturization and the Electronic Manufacturing Service
January 23, 2019 by Philip P. Thurman | News
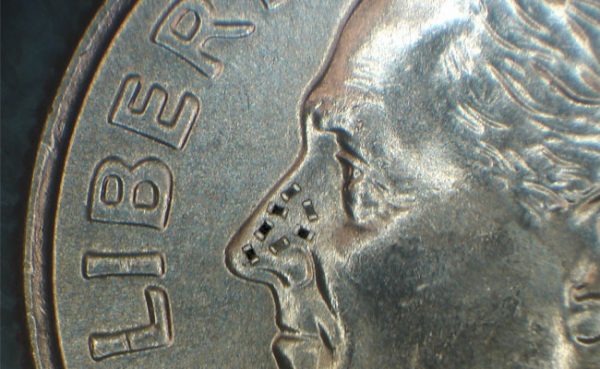
EMS (Electronic Manufacturing Service) value is sustained by the capability to support electronic assembly population using increasingly complex layout densities and geometrically progressive miniaturizing component packages. And, in parallel, continue offering transparent quality levels, responsiveness, and investment return. With Moore’s Law recently decelerating and Dennard Scaling continuing a rigorous technical debate regarding size, cost, and power density constants (Woo, 2016), many smaller, less technically capable EMS providers will be driven into nonexistence resulting from an inability to meet these new technological manufacturing demands. MEMs (Microelectromechnical Systems), smart devices, sensor and tracking technologies, and the IOT (Internet of Things) continue steady market expansion and those EMS providers who cannot or will not adapt will be left fighting for diminishing, low margin legacy scraps. Peter Drucker (Trout, 2006) stated “A business has only two functions: marketing and innovation.” This innovation belongs to the nimble, responsive, and technically capable EMS who can manufacture at parity with the primary assembly driving market force – component and subsequent assembly miniaturization.
The unrelenting drive towards smaller platforms as forced by multiple markets require deep smarts and an EMS recognizing that the electronics industry has evolved into a blend of objective mechanistic processes and subjective organic assembly art. The EMS outsourcing field will also narrow as larger OEMs cannot absorb incurred microelectronics manufacturing overhead or the necessary core competency development investment. This dramatic technological shift will also force many cottage industry EMS providers into nonexistence who will not or cannot innovate in parallel. Legacy product demand and traditional manufacturing technology will not abruptly cease but long term strategic growth cannot occur without proportional intellectual, technical, and cultural capital alignment towards electronics miniaturization.
EMS providers must strategize along the following principles for sustaining value. These five primary attributes will separate those EMS providers struggling to exist or imminently failing and those who will thrive and innovate. While the following elements are also essential for current EMS providers, their necessity will only magnify as the EMS technological miniaturization expectations accelerate:
Capital Equipment with Capable Human Technical Support
As miniaturization and microelectronics assembly evolve, assembly techniques and manufacturing equipment sophistication also demand a corollary increase in precision and repetition. Passive chip components (i.e., resistors, capacitors, ferrite beads, etc.) continue size reductions. As Niemann, et. al. (2017) state:
“…miniaturization leads to new technical requirements of the production processes and to highly integrated electronic systems…(this) leads to a high need of research to help the industry with the integration of these components in their product design and to enable them to establish stable manufacturing processes.”
Consistent and reliable high speed placement of .01005” and even .008004” packages will become as commonplace as .0805” and .0603” packages from previous decades. Manual reworking is no longer relevant when operators cannot even see the requirement without powerful magnification aids, precision goes beyond subjective human intervention, and components have airborne inhalant warnings on reels. Not only must equipment elevate, but the intellectual capital of technical expertise required to properly operate will also require higher proficiency levels. While initial training is fundamental regardless of sophistication, both equipment and technical operators gearing towards microelectronics manufacturing will require both time and capital investments. Passive miniaturization will eventually reach a point where individual components disappear with technologies that David Zogbi (2016) describes as “ceramic multilayered stacking, thin film sputtering, photolithography, and co-firing to achieve continued ultra-small modularization.” Individual discreet components will be replaced with functions sputtered and etched into the circuit. Each EMS must gauge relevant ROI in terms of market position, risk, and opportunity.
Supply Chain Partnerships
Supply Chain Partnerships through standard licensed distributors and even direct OCM channels are vital regardless of manufacturing capability but as larger components become more difficult to source or force sourcing from more high risk alternatives (unlicensed distributors), smaller package device availability and price may become more competitive. Multiple arrangements such as on-site stores, Kanban, and push-pull arrangements may be established to ensure a steady material flow for current and future customer commitments. Distribution profitability is directly tied to an OCM’s ability to meet supply and demand.
Component manufacturers, like any other business, pursue the highest possible profit margins through waste elimination, maximizing efficiency, and expanding shareholder value. The electronics industry already feels the current MLCC shortage impact, drastic inventory reductions of once considered stock components, and consignment arrangements forcing smaller EMS providers into logistical acrobatics for customer order fulfillment. By providing smaller passive component packages such as .0201”s and a .01005”s, OCMs achieve higher profit margins by increasing volume yet apply similar capex and consume the same raw material.
DFM & DFQ Expertise
As current larger components ebb and new platforms are developed, Design for Manufacturing (DFM) and Design for Quality (DFQ) are essential. The scope of obsolescence is no longer restricted to just specific function but also package availability. When an EMS is involved on the assembly or system front end development, advice and layout coaching is critical to the design engineering team for manufacturing optimization. Fundamental solder paste to stencil gasketing interaction is critical to success when solder deposition is defined by solder fine quantity instead of volumetric measurements. While thermal copper balance, trace routing, component to board edge proximities, surface finish, and via configurations are all still important regardless of package sizes, miniaturization makes a comprehensive DFM analyzed assembly that much more critical. Impedance balanced circuits, RF, and copper balancing demand layout optimization for expected performance along with appropriate surface finish and flux/solder chemistries. Mask defined pads, adjacent placement of significantly different size packages, untented vias in pads, and other poor practices can ruin the best of intentions and a well applied DFM partnership may eliminate weaknesses prior to spinning the first fabrication. While embedded components within the printed circuit board substrate is one aspect to address component miniaturization and provides multiple potential benefits (Clemons, 2014), commercial viability is only recently developing and inapplicable to most EMS providers unless design support, printed circuit board fabrication, and manufacturing are all provided in unison, and configuration remains relatively static.
Long-term Partnership Collaboration
As larger, more cumbersome platforms are reengineered towards microelectronic miniaturization, the EMS to customer partnership necessity is magnified. The natural result of a committed professional partnership is enhanced communication. Still adhering to a single point of contact interchange, the EMS can more readily align resources, advise and develop prototype and preproduction, and tighten the DFM/DFQ feedback loop. Not only is heightened communication and expectation clarity enhanced, the shortened communication cycle accelerates qualification for time to market sensitivity. Historical collaboration eliminates misconceptions, offers already developed cultural alignment, and the EMS becomes an extension of the OEM.
Culture of Quality
Regardless of technical sophistication, KPI accountability, or any other performance metric, the quality of a product or service is only as good as the people manufacturing or providing that service. As components and assemblies continue growing beyond human subjectivity to determine conformity during early assembly stages, accountability through personal responsibility will become even more essential to maintaining an EMS’s competitive edge. While Quality Assurance may exist as a departmental name, each associate within the organization IS the quality department. J.M. Juran identified this CWQM (Company Wide Quality Management) where quality is a natural extension of business planning (Juran, 1988) and this model is also a key concept incorporated into the newest ISO9001 Quality Management Standard revision. Executive Management must foster self-managed teams, flatten siloed hierarchies, and encourage corporate matrix structures to supply agility the market demands.
Continuing miniaturization is dynamic, shaping strategic EMS direction for manufacturers, design engineers, and OEMs matching manufacturing equipment necessary to place increasingly smaller components with precision and repetition. As Lefler (2008) states “…if you don’t continue to innovate and make your own products obsolete, then somebody else will.” EMS providers cannot ignore the continuous driving market trend of electronics miniaturization and must adapt both cultures and strategies to sustain continuing and future success. Every EMS must address and acknowledge increasing miniaturization and innovate towards continuing success in the electronic manufacturing market’s ongoing evolution.
Reference:
Clemons, M. (2016). Use Embedded Components to Improve PCB Performance and Reduce Size. Electronic Design. Retrieved from embedded-components- improve-pcb-performance-and-reduce-size
Juran, J.M. (1988). Juran’s Quality Control Handbook. Fourth Edition, New York, NY. McGraw-Hill, Inc. 6.23.
Lefler, P. (2008). Make Yourself Obsolete or Your Competitors Will. Innovation Management.se. Retrieved from http://www.innovationmanagement.se/imtool-articles/make-yourself-obsolete-or-your-competitors-will/
Niemann, Jens & Harter, Stefan & Kaestle, Christopher & Frank, Jorg. (2017). Challenges of the Miniaturization in the Electronics Production on the example of 01005 Components. 10.1007/978-3-662-54441-9_12.
Trout, J. (2006). Peter Drucker on Marketing. Forbes. Retrieved from www.forbes.com/2006/06/30/jack-trout-on-marketing-cx_jt_0703drucker.html#2ba9f3aa555c
Woo, S. (2016). What Comes After Moore’s Law and Dennard Scaling? Semiconductor Engineering. Retrieved from https://semiengineering.com/what-comes-after-moores-law-and-dennard-scaling
Zogbi, D.M. (2016). The Next Generation in Passive Electronic Components. Retrieved from https://www.ttiinc.com/content/ttiinc/en/resources/marketeye/categories/passives/me-zogbi-20160630.html
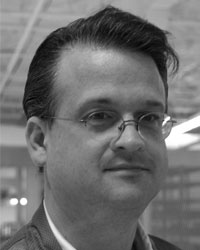
Philip P. Thurman
Phil is currently the Quality Assurance Director for Quality Manufacturing Services, Inc. and has been a manufacturing quality assurance executive for 30 years with extensive experience in military power management systems, electronic manufacturing services, and quality systems applications. Receiving a BA in English from Stetson University and an MBA in Organizational Leadership from Norwich University, he is a published author and often consulted for electronic systems manufacturing development guidance. His extensive knowledge offers unique insights into industry trends, manufacturing advancements, and the continuing role of quality assurance evolution relative to technological progression.